Client in focus
Coastruction: repairing nature with 3D artificial reefs
Help restore damaged reefs with 3D printed artificial reefs. That's Coastruction's mission. Not for nothing did this ambitious startup receive the prestigious V.O. Patents & Trademarks Innovation Award during the NL Startup Competition. We spoke with Josine Beets, Project & Business Development Manager at Coastruction.
Reefs in the oceans are threatened worldwide. As a result, many marine animals and fish species are losing their habitat and the risk of shoreline damage and flooding can increase. “Coastruction designs, manufactures and installs 3D artificial reefs that complement natural reefs. Using 3D printers developed in-house and reef designs with a natural shape, we integrate the reef into the local ecosystem in which the animals live as best we can. Because when important species adopt their new habitat, the chances of success are greater,” says Beets.
From Idefix to Obelix
The foundation for Coastruction was laid in 2015 by founder Nadia Fani. Determined to save coral, she was already experimenting with 3D printing technology as an application for artificial reefs. Beets: “She developed a prototype printer called Idefix. We are now working with a larger printer, Asterix, which can print structures of about 1 cubic meter.” The sequel can be guessed: Obelix is in the works. It will soon be able to print structures of 6 cubic meters.
Layer by layer
“When designing an artificial reef, we look carefully at the environment of the current reef, its forms and the ecosystem surrounding it. Together with experts, such as a specialized biologist in Australia, we determine the best design.” Printing the artificial reef is done layer by layer. Beets explains: “We first make a bed of a dry powder mix. That is a mixture of material from the place where the reef should come. This can be sand or shells from the beach, for example. We mix this material with CEMIII, currently the most responsible form of cement. With nozzles we spray water in the desired form onto the powder bed. The water then activates the cement. After printing each layer, the bed sinks and we add a new layer of dry mix. In this way, the structure is gradually built up with precise adhesion.”
Testing and monitoring
Printing an artificial reef is quite fast: a 1 cubic meter structure can be printed in 3 hours. “After the last layer, we let it cure for another 12 hours or so, and then we clear the structure of excess powder,” Beets continues her explanation. “Then we completely wet the structures so they become even stronger. We tested our prints in-house for strength. We also test it in the Delta flume (Deltares) to see how much energy from the waves is broken on our artificial reef. The most important step after that is the installation of the reef on site. This is done very precisely. After installation, experts monitor the operation of the artificial reef: we see whether algae grow on it and whether fish find their place there.”
Legal protection
Coastruction won the V.O. Innovation Award: a €2,500 voucher. “That came in handy,” says Beets. “We spent it on legal advice. After all, as a small startup in the big world, we had not yet drawn up general terms and conditions for the products we supply. And that made us vulnerable, because our technology, ideas and products are then less protected. With the help of V.O.'s lawyers, we drafted the terms and conditions. Now it is stipulated, among other things, that if you buy a product from us, it does not become the property of the customer until full payment is made. Also, the buyer does not become the owner of intellectual property rights vested in the products. It is also important to Coastruction that our name be mentioned in marketing communications from the buyer about the structures provided. Furthermore, we have set up conditions for if the printed structure is damaged, for example during transport.”
Applications worldwide
The first orders have now been designed and printed from the RDM Innovation Dock in Rotterdam. Coastruction does this worldwide for beach resorts, NGOs and universities, such as TU Delft, among others. But also for offshore companies, such as WECO and TouchWind, who see the application of artificial reef in the foundation of their offshore energy parks. “We have applied for a grant to develop printer Obelix. Certainly if that is in place, we could start making more and more impact. Our ambition is to have our printers available in locations worldwide, close to the reef. And that we train local people to be able to work with them.”
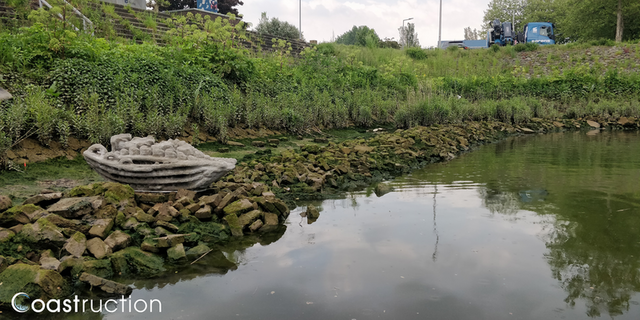
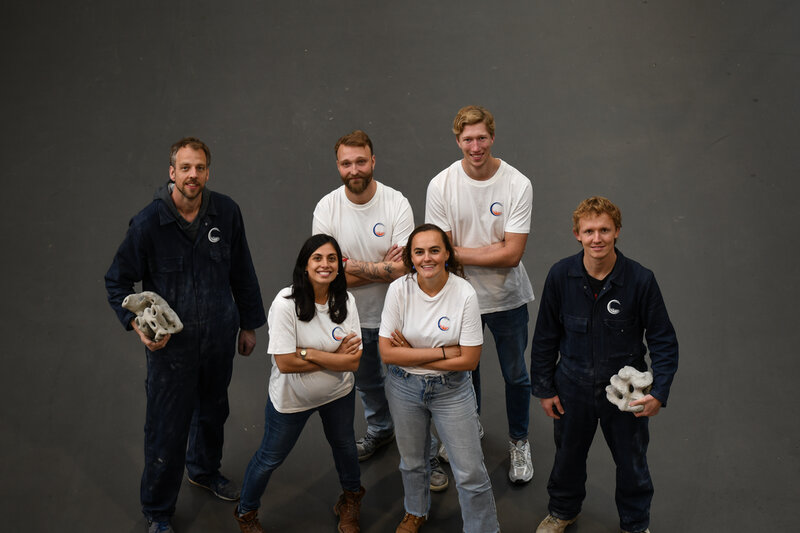
More about Coastruction can be found at
www.coastruction.com/
Share